Hydraulik

Hydraulik (von altgriechisch ὕδωρ hýdor „Wasser“ und αὐλός aulós „Rohr“)[1] bezeichnet die Technik der Verwendung von Flüssigkeiten zur Signal-, Kraft- und Energieübertragung.[2]
Im weitesten Sinne können auch Anlagen zur Nutzung von Wärme- oder Bewegungsenergie oder zum Flüssigkeitstransport als hydraulische Systeme betrachtet werden (z. B. Wasserversorgung, Wasserkraftwerke und Heizungsanlagen sonstige Leitungsanlagen).
Die Lehre vom Strömungsverhalten von Flüssigkeiten ist die Hydromechanik.
Geschichtliche Entwicklung


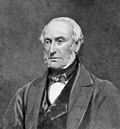

Als Begründer der technischen Hydraulik gilt der Engländer Joseph Bramah. Im Jahr 1795 entwickelte er eine mit Druckwasser betriebene hydromechanische Maschine[3], die nach dem hydrostatischen Gesetz von Blaise Pascal arbeitete und die eingebrachte Kraft 2034-fach vergrößerte. 1851 entwickelte William G. Armstrong den Gewichtsakkumulator, einen Speicher, mit dessen Hilfe große Volumenströme erzeugt werden konnten. Die London Hydraulic Power Company nahm 1882 eine zentrale Druckwasserversorgung für mehrere Hydraulikanlagen in Betrieb.
1905 gilt als der Beginn der Ölhydraulik, als Harvey D. Williams und Reynold Janney[3] erstmals Mineralöl als Übertragungsmedium für ein hydrostatisches Getriebe in Axialkolbenbauart[3] mit Taumelscheibe verwendeten, das sie für Verschiebungen bei einem maximalen Druck von 40 bar einsetzten. Hele-Shaw entwickelte 1910 die erste brauchbare Radialkolbenmaschine.[3] 1929 erhielten die Ingenieure Hans Thoma und Heinrich Kosel ein Patent auf eine Axialkolbenmaschine in Schrägachsenbauart.[4] Die erste Servolenkung entwickelte Harry Vickers (um 1925), das erste vorgesteuerte Druckventil entwickelte er 1936.[3] Jean Mercier baute 1950 in größerem Umfang die ersten hydropneumatischen Druckspeicher.[3] Für die Entwicklung der Servo-Hydraulik waren Arbeiten von John F. Blackburn, Shih-Ying Lee und Jesse Lowen Shearer von Bedeutung, die 1958 in den USA erschienen sind.[3]
Hydraulik zur Kraftübertragung
Hydraulik ist in der Technik eine Getriebeart im Gegensatz zu mechanischen, elektrischen und pneumatischen Getrieben. Sie dient zur Leistungs-, Energie- oder Kraft-/Momentenübertragung von der Arbeitsmaschine (Pumpe) zur Kraftmaschine (Kolben bzw. Hydraulikmotor), wobei die Leistungsparameter auf die Forderungen der Kraftmaschine angepasst werden. Die Hydraulik überträgt die Leistung durch die Hydraulikflüssigkeit, in der Regel spezielles Mineralöl, in zunehmendem Maß aber auch durch umweltverträgliche Flüssigkeiten, wie Wasser oder spezielle Carbonsäureester oder Glycole. Die übertragene Leistung ergibt sich aus den Faktoren Druck und Volumenstrom. Zu unterscheiden sind:
- Hydrodynamische Antriebe arbeiten mit einer Pumpe und einer Antriebsturbine. Die Drehzahl- und Drehmomentwandlung geschieht über die kinetische Energie der Flüssigkeit.
- Hydrostatische Antriebe wandeln primärseitig die mechanische Leistung der Kraftmaschine (Elektromotor, Dieselmotor) durch eine Pumpe (Arbeitsmaschine) in hydraulische Leistung um. Diese Leistung wird in Verbrauchern (Kraftmaschine) wieder in mechanische Leistung umgeformt, und zwar in Hydraulikzylindern in eine lineare Bewegung oder in Hydromotoren in eine Drehbewegung. Hydrostatische Antriebe haben besseren Wirkungsgrad als andere Getriebearten, wenn die abtriebsseitige Geschwindigkeit stufenlos verstellbar sein muss.
Durch das Einleiten von unter Druck stehender Flüssigkeit in den Zylinder werden die darin befindlichen Kolben und Kolbenstangen in lineare Bewegung versetzt, die für Arbeitsvorgänge und zum Antrieb von Maschinen ausgenutzt wird. Auch rotierende Antriebe können durch Flüssigkeitsdruck realisiert werden, etwa mit dem Hydraulikmotor.
Hydraulische Systeme ähneln prinzipiell den Antrieben der Pneumatik, bei der Druckluft zur Kraft- und zur Signalübertragung verwendet wird, haben aber davon abweichende Eigenschaften. So wird in der Ölhydraulik immer ein Kreislauf des Fluids benötigt (Hin- und Rücklauf), während in der Pneumatik die Abluft – meist über einen Schalldämpfer – in die Umgebung abgeblasen wird. Nur bei der Wasserhydraulik wird gelegentlich auf Kreisläufe verzichtet. Gegenüber der Pneumatik hat die Hydraulik den Vorteil, dass wesentlich höhere Kräfte übertragen werden können und sehr gleichförmige und exakte Fahrbewegungen möglich sind, da die Verdichtung der Hydraulik-Flüssigkeit so gering ist, dass sie bei technischen Anwendungen kaum beeinträchtigend wirkt.
Die Kombination von hydraulischen Elementen mit elektrischen Komponenten zur Steuerung wird als Elektrohydraulik bezeichnet.
Vorteile

Die weite Verbreitung in vielen Industriezweigen verdankt die Hydraulik folgenden Vorteilen:
- die aufgelöste Bauweise, das heißt die flexible Verbindung zwischen An- und Abtrieb und eine gute konstruktive Anpassung an Raumvorgaben. Als Verbindung zwischen Motor und Pumpe dienen Rohr- und Schlauchleitungen, die weitgehend frei verlegbar sind. Bei mechanischen Antrieben hingegen ist es notwendig, eine direkte Verbindung zwischen Motor und Getriebe und weiter zu Differential über zum Beispiel eine Kardanwelle, Hardyscheibe, Gelenkscheibe oder eine Kette herzustellen. Daher ist dort die Position des Getriebes durch die Position des Motors weitgehend festgelegt.
- moderne spritzfreie Clean-Break-Schnellkupplungen ermöglichen ein sicheres und sauberes Trennen von Verbraucher und Pumpe. Der Schmutz- und Lufteintrag in die Hydraulikanlage ist gering.
- stufenlose Geschwindigkeitsstellung des Abtriebes in sehr weiten Grenzen, einfache Umkehr der Bewegungsrichtung
- Erzeugung linearer Abtriebsbewegungen mit einfachen technischen Bauelementen bei sehr hohen Wirkungsgraden
- einfache Erzeugung sehr großer Kräfte und Drehmomente
- sicherer und schnell wirkender Überlastungsschutz durch Druckbegrenzungsventil
- hohe Leistungsdichte, das heißt vergleichsweise kleine Bauelemente für große Leistungen, vor allem im Vergleich zu Elektromotoren
- Realisierung parallel arbeitender translatorischer oder rotatorischer Abtriebselemente (Hydraulikzylinder oder Hydromotoren) mit einem Primärteil (Pumpe) in einem gemeinsamen System, dabei ergibt sich die Wirkung eines Differentials ohne weiteren Aufwand
- hohe Lebensdauer, da das Fluid selbstschmierend ist und als Kühlmedium dienen kann
- einfache Regelungskonzepte zur optimalen Ausnutzung des Antriebsmotors bei stark variierenden Leistungsanforderungen der Arbeitsmaschine
- hohe Stellgenauigkeit
- gleichförmige Bewegungen wegen der geringen Kompressibilität der Hydraulikflüssigkeit
- Standardisierung durch Anwendung von genormten Bauteilen, Anschlussmaßen, Einbauräumen usw.
- einfache Anzeige der Belastung durch Druckmessgeräte
- niedrige Induktivität der Hydromotoren und Zylinder
- Anfahren aus dem Stillstand bei Volllast
- schnell (aber bei gleichem Arbeitsdruck langsamer als Pneumatik), feinfühlig, gleichförmig und stufenlos verstellbare Zylinder- und Motorgeschwindigkeiten.
- Reibung in den Aktoren ist durch hydraulische Öle vermindert.
- Korrosionsschutz durch Hydraulikflüssigkeit (außer Wasser)
- kein elektrisches Streufeld der Abtriebe
Nachteile
- Nachteilig bei hydraulischen Antrieben ist die Kompressibilität des Fluids, die unter Druck zur Kompression führt. Hieraus entstehen unter Umständen Druck- und Bewegungsschwingungen. Dieses Problem wirkt sich aber nur bei Antrieben mit hohen Anforderungen an die Gleichförmigkeit der Geschwindigkeit bei stark wechselnden Lasten aus, zum Beispiel Vorschubantriebe an Werkzeugmaschinen. Hier muss mit flexiblen Kupplungen gegengesteuert werden, was die Kosten steigert.
- hohe Anforderung an die Reinheit der Hydraulikflüssigkeit
- Schaltgeräusche der Ventile
- Gefahr von Leckagen, Leckölverluste
- Temperaturabhängigkeit der Hydrauliköle (Viskosität und Energieverlust durch innere Reibung erhöhen sich bei sinkenden Temperaturen)
- Strömungsverluste, die in Wärme umgesetzt werden und die Anlage aufheizen (Energieverlust)
- Schwingungsneigung durch Druckstöße und damit verbundene Geräuschentwicklung
Anwendungen
Hydraulikzylinder mit linearer Bewegung dienen zum Heben von Lasten in Gabelstaplern, Baggern, Aufzügen, Fahrzeugkranen etc.
Mobile Arbeitsmaschinen wie Baumaschinen oder Landmaschinen werden häufig mit Hydraulik-Antrieb ausgestattet.
Fahrzeuge werden oft mit hydraulischen Getrieben bzw. Flüssigkeitswandlern angetrieben, beispielsweise mit so genannten Schrägachsen- und Schrägscheibenmaschinen, mit denen hohe Leistungen übertragen werden können. Mit Hydraulikgetrieben lässt sich die Kraftübertragung eines mit festgelegter Drehzahl arbeitenden Motors flexibel an die Betriebsbedingungen anpassen, so etwa in Automatikgetrieben und hydraulischen Antrieben von Diesellokomotiven.



Weitere typische Anwendungsbeispiele sind:
- Hydraulikschrauber und Bolt Tensioners zur Schraubenvorspannung
- Aufzüge mit geringer Hubhöhe, aber hoher Zuladung
- Kraftfahrzeuge und muskelbetriebene Zwei- und Dreiräder diverser Bauart: Bremsen (Bremsflüssigkeit, auch bei Fahrrad), automatisierte Getriebe, Servolenkung, Fahrwerksregelung, Cabrioverdecke
- Verbrennungsmotor: Nockenwellenverstellung, Ventilbetätigung, Betätigung von Einspritzeinheiten
- Flugzeug: gesamte Steuerung der Flügelklappen (konzipiert während des Zweiten Weltkriegs[5]) sowie Ein- und Ausfahren des Fahrwerks
- Gleisbremsen im Rangierbahnhof
- Landwirtschaft: bei Traktoren, Lenkhydraulik und Kraftheberpaket mit Lageregler zum Heben, Antreiben und Steuern von Arbeits- und Anbaugeräten
- Kfz: Fahrzeuge werden mit Hilfe hydraulischer Hebebühnen angehoben
- Bagger: hydraulischer Antrieb aller Arbeitsgeräte einschließlich Dreh- und Fahrwerk
- Mobilkrane: hydraulischer Antrieb der Teleskopmasten, Hub- und Windwerk, Drehwerk, Abstützung, Lenkung sowie teilweise Fahrantrieb Flurförderzeuge;
zum Beispiel Gabelstapler: alle Bewegungen einschließlich Fahrantrieb und Lenkung - Kletterkrane und Vorschubrüstungen werden hydraulisch gehoben und verschoben.
- Forstmaschinen: hydrostatische Fahr- und Arbeitsantriebe
- Nutzfahrzeuge: Kipphydraulik, Ladebordwände, Lenkhilfen (Servolenkung), Kupplungs- und Bremsenbetätigung, hydrostatischer Fahrantrieb an der Vorderachse (MAN)
- Panzer und Fregatten: hydrostatische Überlagerungslenkung, servohydraulische Richtantriebe für die Hauptwaffe beziehungsweise für die Geschütztürme
- Werkzeugmaschinen: Haupt- und Hilfsbewegungen an Pressen, Scheren und Abkantmaschinen; Vorschubbewegung an Schleifmaschinen, Betätigungsfunktionen wie Werkzeugwechsler, Werkstück- und Werkzeugspannung und Achsenklemmung an allen spanenden Werkzeugmaschinen. Dabei kann die Kraft durch Druckwandler vervielfacht werden.
- Handwerkzeug, das besonders hohe Kräfte erzielt: zum Schneiden von Drahtseil, Verpressen von Seilklemmen, Wasserrohr-Fittings, Elektro
- Metallurgie: Antriebe an Elektro- und Hubbalkenöfen; Stranggießanlagen, Chargier- und Kühlbetten
- Walzwerke: Walzspaltregelungen (Regelung der Dicke des gewalzten Materials mittels sog. hydraulischen Anstellzylindern); alle Hilfsbewegungen für die Zuführung des Walzgutes; Richt- und Scherantriebe
- Stellantrieb: elektrohydraulische Regelung von Fluiden (Druck, Durchfluss) in der Verfahrenstechnik, Kraftwerke, Pipelines
- Bergbau: Zylinder im Schreitausbau, hydrostatische Antriebe in Gewinnungsmaschinen und Vortriebsmaschinen
- allgemein: Hydraulikstempel zum Bewegen schwerer Lasten z. B. in der Baubranche zum Vorschub und Einbau von Brückenträgern und sonstigen schweren Fertigteilen, bei Schwerlasttransporten oder auch als Rettungsgerät bei THW und Feuerwehr
- Automobilzulieferer: zum Tiefziehen von Motorhauben, Kotflügeln oder anderen Karosserieteilen
- Fahrradbau: Hydroforming von Aluminiumrohr als Teil des Rahmens, mittige Aufweitung des Lenkerrohrs
- Feuerwehr: Bei der Feuerwehr wird der hydraulische Rettungssatz, der unter anderem aus Rettungsspreizer, Rettungsschere und Rettungszylinder besteht, verwendet, um Personen aus deformierten Fahrzeugen zu retten.
- Bei schnelllaufenden Maschinen (wie etwa Turbinen) werden zur Versorgung der Lager mit Schmier- und Kühlstoffen Hydraulikpumpen verwendet, die die Flüssigkeiten über Hydraulikleitungen zur Versorgungsstelle fördern.[2] Über getrennte Druckleitungen fließt das Öl zur Pumpe zurück.
- Katapultantriebe bei Achterbahnen:[6] Hydrauliköl wird in mit Stickstoff gefüllte Speicherzylinder gepumpt, der Stickstoff wird komprimiert. Nach der Freigabe zum Abschuss wird das unter Druck stehende Öl in viele kleine Hydraulikmotoren geleitet, die über ein Getriebe eine Seilwinde antreiben. Der im Seil eingehakte Zug wird katapultartig beschleunigt.
Hydraulische Handpresse

Durch die hydraulische Presse kann mit geringer körperlicher Kraft eine große Kraftwirkung erzielt werden. Durch manuelles Pumpen am Pumpkolben (2) eines Kfz-Wagenhebers kann am Presskolben (3) eine tonnenschwere Last gehoben werden.
Funktionsbeschreibung: Wird der Pumpkolben (2) nach unten gedrückt, schließt das Ventil (4) und das Ventil (5) öffnet, damit strömt Hydrauliköl in den Presszylinder. Der Presskolben (3) hebt sich. Wird der Pumpkolben nach oben bewegt, öffnet das Ventil (4) und das Ventil (5) schließt. Dadurch kann aus dem Vorratsbehälter (1) Hydrauliköl nachfließen. Wirkt auf den Pumpkolben mit einer Fläche von 0,5 cm² eine Kraft von 100 N (entspricht einer aufgelegten Masse von etwa 10 kg), ergibt das einen Druck von
- .
Dieser statische Druck wirkt auch im Presszylinder. Hat der Presskolben eine Fläche von 40 cm², wirkt auf ihn eine Kraft von
- ,
womit man etwa 800 kg hochheben kann. Um den Presskolben gegen diese Last um einen Zentimeter nach oben zu drücken, muss ein Volumen von 40 cm³ bewegt werden. Dazu sind mehrere Pumphübe von zusammen 80 cm notwendig. Die hydraulische oder Druckenergie beträgt
- .
Diese Energie ist gleich der Arbeit, die am Pumpkolben aufgewendet und vom Presskolben verrichtet wird:
Schaltsymbole und Schaltungen
- Schematische Darstellung
- Schaltplan
Ein Schaltplan ist der Plan einer hydraulischen Anlage. Die Bauteile sind durch genormte Symbole dargestellt. Diese Pläne sind Teil der zu jeder Anlage erforderlichen Dokumentation, wichtig insbesondere zum Erstellen und Warten der Anlage. Die Liste der Schaltzeichen (Fluidtechnik) enthält eine umfangreiche Aufstellung von Symbolen für Hydraulik und Pneumatik, so Schaltzeichen für Speicher, Filter, Pumpen und Kompressoren, Zylinder und Ventile.
Schaltpläne können individuell, firmenspezifisch oder nach Normen (DIN ISO 1219) erstellt werden. Sie können Teile wie z. B. Arbeits- und Steuerschaltkreise, die Schritte des Arbeitsablaufs, die Bauteile der Schaltung mit ihrer Kennzeichnung sowie die Leitungen und Verbindungen darstellen. Die räumliche Anordnung der Bauteile wird in der Regel nicht berücksichtigt.
Ein Symbol zeigt ausschließlich die Funktion eines Bauteiles bzw. Gerätes, es sagt nichts über den konstruktiven Aufbau und Einbaulage der Hydraulik-Komponenten aus. Symbole werden einfarbig dargestellt, und im Normalfall werden sie unbetätigt, stromlos bzw. in Ausgangsstellung dargestellt. Zur Modellierung können Beziehungen wie die Elektro-Hydraulische Analogie verwendet werden.
Gefährdungen
Aufgrund von Druckimpulsen, Verschleiß, Alterung, Beschädigung, schadhafter Einbindung und anderen Faktoren stellen Hydraulik-Schlauchleitungen eine besondere Gefährdung dar. Dazu gehören folgende Risiken:
- gefährliche Maschinenbewegungen durch unzureichende Schutzeinrichtungen, ungenügendes Steuerungskonzept, Bauteilversagen, unbeabsichtigtes Betätigen, Restenergie, Druckabfall, Druckverlust, Ausfall und Wiederkehr von Energie;
- Aufpeitschen von Schlauchleitungen durch falsche Auswahl oder geringe Qualität der Schlauchleitung oder äußere Einwirkungen;
- Wegschleudern von Teilen durch Druckabfall, z. B. an Spannfuttern, unzulässige Druckerhöhung (Bersten von Bauteilen);
- Austritt von Druckflüssigkeit, insbesondere als dünner Strahl unter hohem Druck durch unzulässige Druckerhöhung, Bauteilversagen, äußere Einwirkungen;
- Brandgefahr;
- Haut- und Augenkontakt mit Druckflüssigkeiten;
- Einatmen von Sprühnebel.[7]
Der Betrieb von Hydraulik-Schlauchleitungen erfordert umfangreiche Sicherheitsmaßnahmen. Betreibende müssen im Rahmen einer individuellen Gefährdungsbeurteilung alle nötigen Maßnahmen ermitteln und umsetzen. Ein wichtiger Faktor zur Gewährleistung der Sicherheit der Beschäftigten beim Umgang mit Hydraulikanlagen ist die Prüfung der verwendeten Hydraulik-Schlauchleitungen. Prüfungen sind nötig nach Montage und vor erstmaliger Benutzung, nach Unfällen, längeren Zeiträumen der Nichtbenutzung und besonderen beanspruchenden Ereignissen (Kollisionen, Naturereignissen, Überhitzungen) sowie in festgelegten regelmäßigen Abständen.[8] Weitere typische Maßnahmen sind Schutzüberzüge und Schlauchfangsicherungen für Schlauchleitungen, Sicherheitsventile beim Einsatz von Druckbehältern oder Ölwannen zum Auffangen der austretenden Fluide.[9]
Siehe auch
Literatur
- Horst Beer: 100 Jahre Entwicklung und Einsatz der Hydraulik im Osten Deutschlands. Ein Beitrag zur Technik- und Industriegeschichte. GNN-Verlag, Schkeuditz 2008, ISBN 978-3-89819-240-8.
- H. Exner, R. Freitag, H. Geis, R. Lang. J. Oppolzer: Der Hydraulik Trainer. Band 1: Hydraulik – Grundlagen und Komponenten. 3. überarbeitete Auflage. Herausgegeben von Bosch Rexroth AG. Mannesmann Rexroth, Lohr 2002, ISBN 3-933698-30-8.
- D. Merkle, K. Rupp, D. Scholz: Elektrohydraulik. Grundstufe. Springer, Berlin u. a. 1997, ISBN 3-540-62087-7.
- D. Merkle, B. Schrader, M. Thomes: Hydraulik. Grundstufe. Springer, Heidelberg u. a. 1997, ISBN 3-540-62091-5.
- Dieter Will (Hrsg.): Hydraulik. Grundlagen, Komponenten, Schaltungen. 3. neu bearbeitete und ergänzte Auflage. Springer-Verlag, Berlin u. a. 2007, ISBN 978-3-540-34322-6.
- Helmut Wetteborn: Hydraulische Leitungstechnik: ein Praxis-Handbuch. 1. Auflage, Hansa-Flex, Bremen 2008, ISBN 978-3-88808-703-5.
Weblinks
Einzelnachweise
- ↑ griechisches substantiviertes Adjektiv υδραυλική [τέχνη] hydrauliké [téchne] „die hydraulische [Technik]“.
- ↑ a b Hydraulik und Schmierung für tonnenschwere Turbinen ( vom 30. Juni 2015 im Internet Archive)
- ↑ a b c d e f g Wolfgang Backé: Grundlagen der Ölhydraulik, Institut für hydraulische und pneumatische Antriebe und Steuerungen der RWTH Aachen, 1974, S. 2f.
- ↑ Matthies, Renius: Einführung in die Ölhydraulik, S. 20.
- ↑ Spruce Goose Rules: How the Hughes H-4 Hercules Set Aviation History (With Just 1 Flight), The National Interest, 6. April 2019
- ↑ Coastersandmore.de - Achterbahn Magazin: Achterbahntypen von A wie Accelerator bis Z wie Zac Spin: Antriebe. Abgerufen am 4. Juli 2020.
- ↑ Institut für Arbeitsschutz der Deutschen Gesetzlichen Unfallversicherung (IFA): Sicherer Umgang mit hydraulischen Anlagen – Information des IFA. Abgerufen am 11. Juli 2023.
- ↑ Deutsche Gesetzliche Unfallversicherung e. V. (DGUV): DGUV Regel 113-020 – Hydraulik-Schlauchleitungen und Hydraulik-Flüssigkeiten – Regeln für den sicheren Einsatz. Abgerufen am 11. Juli 2023.
- ↑ Institut für Arbeitsschutz der Deutschen Gesetzlichen Unfallversicherung (IFA): Themenfeld Hydraulik, Pneumatik. Abgerufen am 11. Juli 2023.
Auf dieser Seite verwendete Medien
Autor/Urheber:
- Hydraulic_circuit_directional_control.png: user:duk
- derivative work: Bukk
Hydraulischer Kreis, Richtungssteuerung
Reynold Janney
PORT-AU-PRINCE, Haiti (Feb. 6, 2010) Builder 2nd Class Andrej Paskevic, assigned to Underwater Construction Team (UCT) 1, drills guide holes into a damaged section of pier at the port in Port-au-Prince. UCT-1 and U.S. Army divers are conducting repair operations in the main seaport during Operation Unified Response after a 7.0 magnitude earthquake caused severe damage in and around Port-au-Prince, Haiti Jan. 12. (U.S. Navy photo by Mass Communication Specialist 2nd Class Chris Lussier/Released)
Autor/Urheber: btr, Lizenz: CC BY-SA 2.5
Zusammenstellen eines Schwertransports (Transformator eines Energieversorgers)
Autor/Urheber: LosHawlos, Lizenz: CC BY-SA 3.0
Ein Zweiwegebagger auf Baustelle (Umbau der Straßenbahn-Haltestelle Am Aubuckel in Mannheim-Feudenheim)